In the first quarter of 2022, the European Union launched a strategy to reduce hydrogen costs. The focus is on expanding the production of renewable hydrogen, building partnerships, and supporting pilot projects. Part of the strategy aims to lower hydrogen production costs (HPC), particularly for production via water electrolysis using renewable energy. In English, this is referred to as Levelised Costs of Hydrogen (LCOH) – an abbreviation that can easily be confused with Liquid Organic Hydrogen Carrier (LOHC) when read quickly.
Hydrogen production costs – what’s included? Hydrogen production costs are a key metric for assessing the economic viability of hydrogen production pathways. This figure includes the total costs associated with hydrogen production, i.e. capital expenditures, operating costs, and electricity costs, all relative to the total amount of hydrogen produced over the project’s lifetime. Not included in the HPC are trading margins and transport.
Only when investors, policymakers, and industry stakeholders have knowledge of hydrogen production costs can they make informed decisions about the deployment of green hydrogen technologies and infrastructure. These costs enable direct comparisons between different hydrogen production methods, such as electrolysis powered by solar or wind energy, and help identify opportunities for cost reduction. Moreover, hydrogen production costs provide a benchmark for assessing the competitiveness of green hydrogen compared to other energy carriers and fuels, including fossil-based hydrogen production methods.
Sectors with high decarbonization potential are particularly cost-sensitive. These include heavy industry (including steel production), transportation (especially long-haul freight, shipping, and aviation), ammonia and fertilizer production, energy storage, as well as refineries and the chemical industry (replacing fossil-based hydrogen).
Six key factors The main factors influencing HPC are: 1) electricity price, as it accounts for the largest share of operating costs, 2) capital expenditures (CAPEX), including balance of plant (BOP), 3) ongoing operating costs (OPEX) such as maintenance and water, which affect profitability, 4) higher electrolyzer efficiency reduces electricity demand per kilogram of hydrogen, 5) more operating hours lower specific production costs, and 6) low-cost financing (e.g. through subsidies) significantly reduces annual capital costs and thus the LCOH.
Electricity costs: Electricity is typically the largest cost component in water electrolysis. HPC decreases significantly when electricity comes from low-cost renewable sources (e.g. solar, wind, etc.).
CAPEX (capital expenditures): Investment costs related to the acquisition of equipment are also significant. In addition to core components such as electrolyzers, compressors, storage systems, and hydrogen production infrastructure, water treatment systems and balance of plant (BOP) equipment must also be considered (e.g. hydrogen purification, dryers, cooling, deoxidation, and water deionization systems). CAPEX includes the weighted average cost of capital (WACC), which typically comprises the interest rate, inflation expectations, and investment risk; a higher WACC increases the annualized capital costs and thus raises the HPC.
OPEX (operating costs): These include costs associated with the operation and maintenance of the plant, as well as water consumption and the purchase or lease of land. Although electricity costs are technically part of OPEX, they are considered separately due to their significance.
Electrolyzer efficiency and type: Technologies such as PEM, AEM, and SOEC differ in performance and cost. Higher efficiency reduces specific electricity costs.
Utilization rate: Plants with more operating hours per year achieve better capital cost amortization.
Policy incentives: Tax breaks and other subsidies can significantly improve the economics of renewable hydrogen.
Estimating HPC The equation below can be used to estimate HPC in €/kg:

The equation accounts for annualized capital expenditures (CAPEX). Initial investments are distributed over the calculated plant lifetime. These are typically not fully paid upfront by the investor but are financed through loans with repayment and interest. For these cost components incurred during the project, the weighted average cost of capital is used to appropriately reflect the time value of money.
Subsidies and incentives are factored into the HPC calculation by reducing either CAPEX (e.g. through investment grants) or OPEX (e.g. through lower electricity prices or grid fees). This reduces the annualized costs and thus the HPC, which can significantly improve the economic viability of hydrogen projects. The HPC provides valuable information about the average price at which hydrogen must be sold to ensure financial viability.
Cost factor no. 1: electricity Estimated production costs for renewable hydrogen in 2024 ranged from €6.0 to €14.2/kg in European countries such as Germany, Greece, and Poland, reflecting the significant impact of renewable energy costs, capital expenditures, and the lifetime of the electrolyzer technology used. According to the “European Hydrogen Index 2025” by Ernst & Young, analysts expect HPC to fall below €3/kg by 2030 if electricity prices drop below €50/MWh. However, this remains a challenge for many European countries where electricity costs are currently trending upward.
Cost factor no. 2: electrolyzer After electricity, the second main cost driver for green hydrogen production is typically the acquisition cost of the electrolyzer. Although AEM and PEM electrolyzers have reached a high level of technological maturity, they play a key role in both capital and operating costs. However, the International Renewable Energy Agency (Irena) has predicted that their costs will fall by 80% by 2050.
How to reduce costs? To achieve the €3/kg target, a combination of strategies must be applied. Particularly important are:
• Scaling up manufacturing: larger-scale production of electrolyzers can reduce capital costs
• Innovative technologies: improved catalysts, membranes, and system designs can increase efficiency and reduce costs
• Subsidies: continued government support through tax incentives, grants, and public-private partnerships is essential
• Suitable locations: colocating electrolyzers with renewable energy sources minimizes transmission and grid costs
Using directly connected PV and wind farms could create a pooling effect in electricity supply, thereby lowering HPC. A pooled system could require fewer electrical components for the balance of plant, reducing overall system costs, as shown by a comparison of on-grid and off-grid systems in Sweden. However, further research is needed to assess and analyze the impact of fluctuating electricity load profiles on the performance and lifecycle of electrolyzers when operated exclusively with directly connected PV systems and wind turbines.
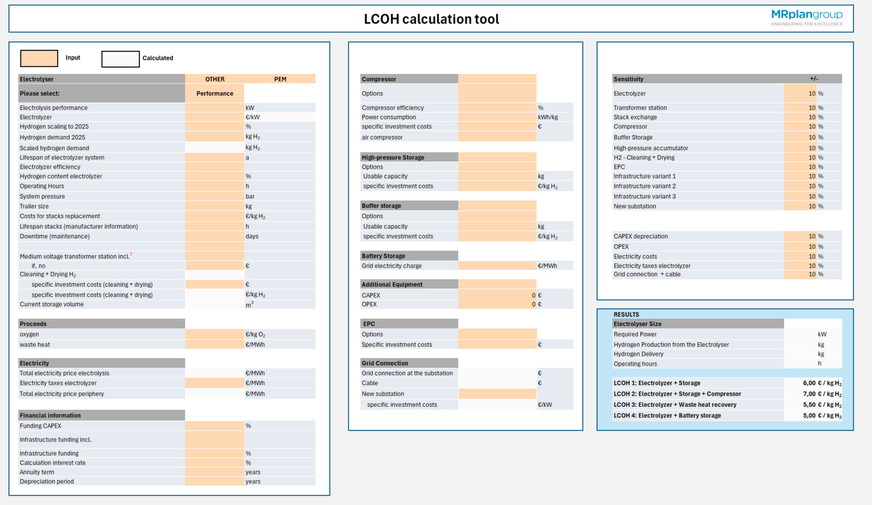
© MR Plan
MR Plan tool includes “soft” costs Although R&D initiatives aim to reduce the CAPEX and OPEX of core systems to facilitate commercial implementation, it is important to consider so-called “indirect costs.” Indirect costs include, among others, site preparation (construction infrastructure, utilities, and electrical connections), permitting, commissioning, and transport. These expenses may be comparable to capital expenditures.
Indirect costs are gaining importance in financial analyses for sustainable hydrogen production, as shown by a study from the U.S. Department of Energy. Analysis tools such as the HPC Excel tool developed by MR Plan enable a comprehensive economic assessment of various electrolyzer technologies based on reliable and up-to-date references. An integrated database allows users to select electrolyzer types and main components according to their requirements. System sizes, auxiliary equipment (such as compressors, medium- and high-pressure storage, transformers), as well as infrastructure costs (e.g. permitting, integration, and EPC), and potential revenues from the sale of heat and oxygen are also included in the calculation.
In addition, the tool allows different project scenarios – with or without subsidies – to be simulated. It is also possible to integrate additional components such as battery storage. The results are clearly presented in a waterfall diagram that visualizes the impact of individual cost factors on the hydrogen price and supports user-specific adjustments.
Therefore, incorporating soft costs from past and ongoing installations will improve the overall understanding of electrolyzer economics and help identify potential barriers to deployment.
Value contribution of planning and engineering firms to reducing HPC A specialized planning or engineering firm can provide valuable support by identifying suitable sites with optimal renewable resources and sufficient water availability, developing detailed financial models, scenario analyses, and risk assessments, selecting the appropriate electrolyzer technology, and assisting with compliance with local regulations and permitting. It can also plan the integration of hydrogen into existing grid, water, and transport infrastructures and prepare reports or pitch decks for potential financing partners – all of which contribute to reducing HPC. These services ensure that projects are not only technically feasible but also economically robust and investment-ready.