Unfortunately, it is not possible to look inside the cells of PEM electrolyzers. But cell voltage is a reliable indicator that can be used to assess the health of individual cells. This requires new concepts for stack design and for monitoring cell voltage. Stack manufacturer Hystar aims to integrate cell voltage measurement as standard in its gigawatt-scale production together with Smart Testsolutions.
Cell voltage indicates aging The electrochemical process, and thus the hydrogen yield, is highly sensitive to cell voltage. Various gradual processes affect the cell over its lifetime. For example, the precious metal catalyst that promotes the splitting of water molecules can lose its effectiveness over time due to so-called catalyst poisons. These are impurities that settle on the surface of the precious metal. Cracks or so-called pinholes can also form in the membrane, allowing hydrogen to pass through.
Many of these processes are reflected in changes in cell voltage. Electrolysis theoretically begins at a cell voltage of 1.48 V. The cells are usually operated at higher voltages, which result from the total voltage of the stack divided by the number of cells. If the resistance in the membrane increases, the voltage also increases at constant current. At some point, the cell leaves the specified voltage window and undesirable chemical reactions occur that damage the cell.
Cell voltage therefore provides information about how “healthy” the cell is and how long it is likely to last.
Cell monitoring as standard In their laboratories, manufacturers of electrolyzers and fuel cells monitor the voltage of each individual cell to better understand the electrochemical processes during development. In series devices, manufacturers usually do not afford this luxury. Typically, only a few cells are measured at random, or only the total voltage of the stack is recorded. However, this value only provides a very rough indication of the condition of the electrolyzer. Ideally, the voltage of each individual cell would be known.
Even when talking about series devices, it should be noted that electrolyzers are still usually custom-built for specific projects, such as a 5-megawatt plant from Hystar in Poland. However, this is currently changing. For example, Hystar is currently completing the setup of its automated production line with a capacity of 4.5 GW. The company recently received approval for €26 million in funding from European sources (EU Innovation Fund) for this production line. “We want to build electrolyzer systems from standardized components like Lego,” says product manager Jan Schmidt. This also applies to cell voltage monitoring, where Hystar, as the manufacturer, monitors each individual cell.
Cell contacts for ultra-compact electrolyzers This is where suppliers like Smart Testsolutions come in. The specialist in measurement technology and test applications has been developing solutions for Cell Voltage Monitoring (CVM) for fuel cells for over 30 years, which are now also being used in Hystar’s electrolyzers. A CVM system measures cell voltage with millivolt precision. It includes cell contacting (Cell Voltage Pickup, CVP), the mechanical system for placement on the stack, and the wiring harness. For the CVPs, the Stuttgart-based company has developed delicate cell contacts that create an absolutely secure electrical and mechanical connection, even though the cells in fuel cells – and now also in Hystar’s electrolyzers – are barely thicker than one millimeter. “Thanks to our experience with fuel cells, our CVPs are a perfect fit for Hystar’s compact electrolyzers,” emphasizes Norbert Witteczek, Business Line Manager e-Cell Electronics at Smart Testsolutions.
The company has also come up with something new for the “wiring harness.” Instead of connecting each cell contact with an individual wire as is usually done, so-called flex boards – flexible printed circuit boards – are used here. These are compact and flexible with virtually unlimited service life – unlike the hundreds of individual wires that have to be cut and crimped by hand.
Service interval indicator for operators For Norbert Witteczek, the collaboration with Hystar is exemplary because the engineers from Norway approached Smart Testsolutions at an early stage. Unfortunately, this is the exception, says Witteczek: “We recommend that all manufacturers of electrolyzers consider cell voltage monitoring early in the design process and get in touch with our team.” 
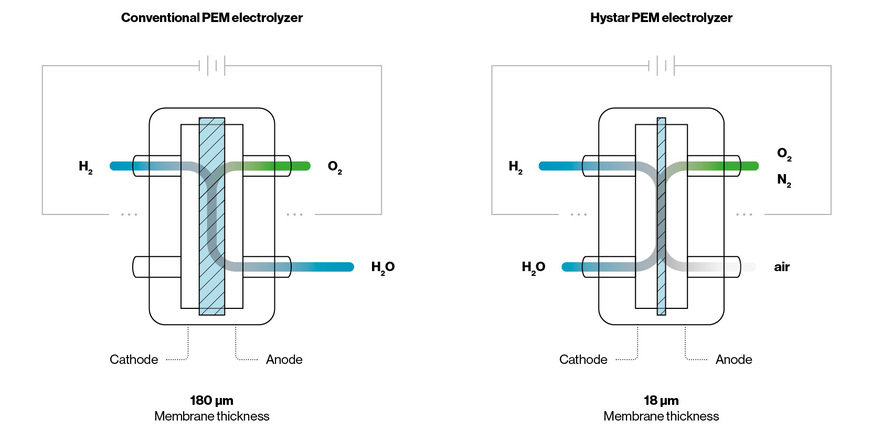
© Hystar
Thin membrane, high efficiency
The Norwegian company Hystar claims to produce the world’s most efficient stack for PEM electrolyzers – primarily due to the thin membrane.
With its patented process, Hystar has found a way to reduce the thickness of the membranes in PEM electrolyzers from the usual approximately 180 micrometers to 18 micrometers. Water is supplied on the cathode side, leaving the anode side free. This allows the anode side to be flushed and potential hydrogen leaks through the membrane to be diluted. This enables safe control of hydrogen diffusion through the membrane and allows the membrane thickness to be reduced, which in conventional systems is used as a diffusion barrier. Hydrogen is still produced on the cathode side, as in conventional PEM electrolyzers. The thin membrane significantly reduces the resistance to hydrogen production and thus increases the efficiency of the cell and the entire stack.
By actively controlling the hydrogen concentration on the anode side, the risk of an oxyhydrogen reaction between hydrogen and the oxygen produced on the anode side is reduced to an absolute minimum. “This makes our stack the safest on the market,” explains Jan Schmidt, product manager at Hystar.
Another advantage of the thin membrane in Hystar’s electrolyzers is that the cells resemble those in fuel cells and can be processed using the same machines. “This allows us to use the existing supply chain for fuel cells also for electrolyzers, and to scale up production more quickly and with less capital to meet growing demand,” says Jan Schmidt.
Hystar product manager Jan Schmidt with the stack modules. Each module contains four stacks that together produce 500 Nm³ H₂/h or 46 kg H₂/h. This is comparable to a process output of 2.5 MW from conventional suppliers. The integrated sensor system also includes CVM from Smart Testsolutions.