The transportation and storage of renewable energy is one of the biggest challenges of the energy transition. One solution is emerging in connection with technologies related to hydrogen as an energy source. The construction of Hydrogen Terminal Braunschweig will create a location for pooling research expertise along the H2 value chain in the megawatt range. The project, funded by the German Ministry of Education and Research (BMBF) with a total funding volume of over 20 million euros, is being implemented as a joint project under the leadership of the Steinbeis Innovation Center Energieplus (SIZ Energieplus), the Technical University of Braunschweig and the University of Hamburg together with the project partners BS Energy and the Fraunhofer Center for Applied Nanotechnology (CAN).
Motivation for the project
The heart of the project is currently the AEM multicore electrolyzer from Enapter with a power class of 1 megawatt, which is the world's first prototype to bring AEM (Anion Exchange Membrane) technology to Braunschweig. In addition, STOFF2's innovative zinc intermediate-step electrolysis system for hydrogen production is to be installed on the site in the coming months. In addition to the electrolyzers located outside the building, electrolysis test benches have been set up in the research building to investigate alkaline electrolysis and PEM (Proton Exchange Membrane) electrolysis.
With the various electrolysis technologies, the essential range of existing production approaches for green hydrogen is represented for direct comparison within the hydrogen terminal. As part of the project, research is being carried out to increase the efficiency of all technologies. In addition, the production of hydrogen by (co-)pyrolysis of hydrocarbon-containing feedstocks is being tested and further developed as part of the research project.
Status quo in implementation
The green hydrogen generated with renewable electricity from the electrolyzers is used in various ways. On the one hand, it is used in internal test benches to carry out ageing tests on fuel cell and electrolysis membranes. Secondly, other external (fuel cell) test benches at the Fraunhofer Center for Energy Storage and Systems (Fraunhofer ZESS) and the Niedersachsen Research Center for Automotive Engineering (NFF), which is around one kilometer away, are supplied with the green hydrogen via pipeline.
Parallel to the supply of hydrogen, Fraunhofer ZESS is supplied with waste heat from electrolysis. For this purpose, the temperature level of the waste heat from the electrolysis processes is raised using a high-temperature heat pump and made available via a local heating network. In addition to the use of the hydrogen in the test benches, it is used to test hydrogen storage in the world's largest metal hydride storage facility, currently operated by GKN Hydrogen.
In addition to being used in test benches, the hydrogen produced on the Hydrogen Terminal site is used to operate a hydrogen refueling station from the manufacturer Maximator. At this filling station, heavy-duty vehicles can be refueled with green hydrogen at a pressure level of 350 bar.
The project is also investigating how the electrolyzers and fuel cells, in conjunction with a large battery storage system (storage capacity: 1.1 MWh) and the solar system, can be used to stabilize the grid when conventional fossil fuel power plants are no longer available.
After the opening ceremony in late summer, the time-consuming commissioning work was then carried out. The high-temperature heat pump from Combitherm, which was designed together with the TGA planner EGS-plan from Stuttgart, is already in operation, as are the redundant propane heat pumps from Viessmann. The ventilation system from Trox and the electrolyzer from Enapter are currently being put into operation. The certified system builder H2 Core Systems from Heide is also being trained on this system and will be able to carry out the construction and commissioning of the Nexus1000 independently in future.
The battery system will be put in operation by SMA by the end of the year. They are working together with the marketer Next Kraftwerke and the Elenia Institute for High Voltage Technology and Energy Systems to investigate the grid-forming properties for voltage and frequency stabilization of the inverter.
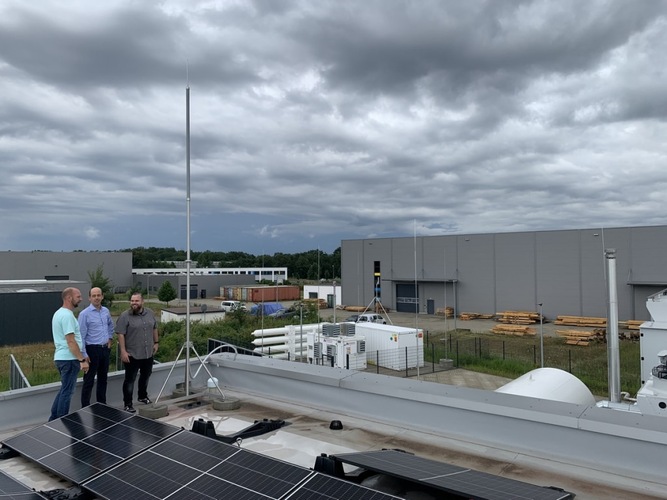
Fig. 2: Markus Hartwig (right) and David Sauss (left) with Sebastian Sipp, Managing Director of STOFF2, on the site of the hydrogen terminal in Braunschweig, Source: STOFF2
Green hydrogen with PV on site
In addition to the now mandatory solarization of the roof areas, an agrivoltaic system was installed on the remaining ecological compensation area as a demonstration. Concrete foundations were completely dispensed with and screw anchors were used. This means that the ground-mounted photovoltaic system can be completely dismantled and is also suitable for temporarily usable areas. The amount of electricity generated is not sufficient to cover the electricity requirements of the systems; therefore, currently for the start of operation, certified green electricity is being purchased on the spot market.
In the future, a 3 MWpeak ground-mounted photovoltaic system will be built on the neighboring property. Empty conduits have been laid for this as well as a feed-in field in our medium-voltage customer system. In the long term, direct, local renewables will not be sufficient for green hydrogen certification. To this end, they will conclude further direct supply contracts (PPAs) in order to achieve the necessary full-load hours and production volumes.
Expansion to include intermediate zinc electrolysis
STOFF2 and SIZ Energieplus are currently investigating the integration of a zinc intermediate-step electrolysis on site. This is a new and innovative electrolysis technology. It takes in green electricity over four hours, stores the energy safely in the form of zinc in the electrolyzer and then discharges green hydrogen over 12 to 24 hours. The charging and discharging process can be flexibly controlled. This ensures that, on the one hand, electricity from renewable energy sources is charged when it is available at low cost and, on the other hand, hydrogen is made available exactly when customers need it.
At the hydrogen terminal site in Braunschweig, the zinc intermediate-step electrolysis is intended to further improve H2 supply security in conjunction with the other components. At the same time, this technology is intended to increase the degree of self-consumption of PV electricity.
Hydrogen Terminal Braunschweig has created an innovative learning, training and research environment for hydrogen, which other projects can now dock onto.
Authors: David Sauss, siz energieplus, Braunschweig, Markus Hartwig, STOFF2, Berlin