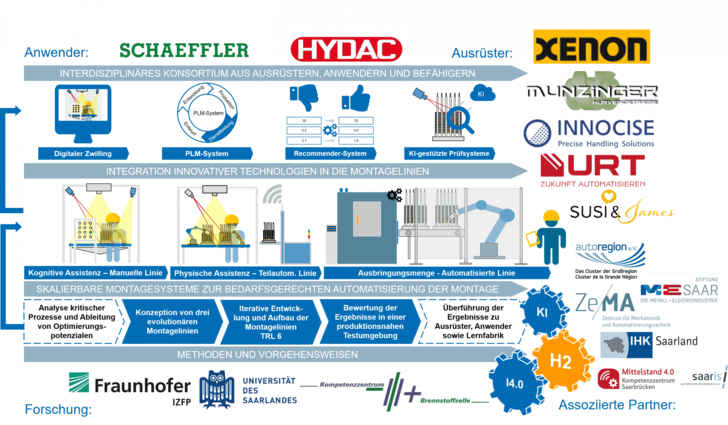
However, as the demand for fuel cells is currently low, this leads to a low utilization of fully automated production systems which in turn results in the payback periods for these pieces of equipment being unviable . Because the demand for fuel cells, and by extension also fuel cell stacks, is expected to fluctuate in the short term and increase sharply in the medium term, assembly systems need to be developed that are easily scalable with regard to output quantity and payback time.
Running alongside this problem is the issue that future refinements to the product are also likely. It is anticipated that such changes will not only affect the geometry of the individual components and the overall system but will influence the type of materials used and the system architecture as a whole. This makes it difficult to perform a simple reconfiguration and thereby hinders the use of the assembly systems for subsequent product generations. Consequently, it is vital to develop assembly systems that both offer the necessary scalability and address the issues of adaptability and reconfigurability.
If we turn our attention to the human factor, it is worthwhile noting that the individual processes involved in fuel cell assembly are often performed by highly qualified technicians who are put under significant strain due to the high degree of product variability, the complex process steps and the high quality expectations for the product. Therefore the assembly systems need be designed with people at their center while also allowing for a certain degree of automation. This includes the consideration and integration of both cognitive and physical assistance systems. Such an approach makes it possible to relieve the mental and physical burden while also involving staff at a shifting level of expertise.
Authors: Rainer Müller, Lennard Margies & Klaus Fabian - All from ZeMA - Zentrum für Mechatronik und Automatisierungstechnik gemeinnützige GmbH, Saarbrücken