PV modules glisten in the sun and wind turbines turn in a light breeze as about a dozen CEOs and managing directors of energy supply companies from Switzerland arrive at the Enertrag hybrid power plant in the Uckermark region. They want to learn from the experiences in Brandenburg. The hybrid power plant is located in a scenic landscape of fields, forests and lakes in the Federal State of Brandenburg, runs entirely on renewable energy and has a rated capacity of 2.6 gigawatts.
Spread over an area of 40 by 40 kilometers, solar and wind power plants generate electricity that is either used directly, stored or converted. Smaller, dedicated substations collect the self-generated electricity before it is fed into the central Bertikow substation and the public grid. If more green electricity is generated than consumed, it is directed to electrolysis to produce hydrogen or to a wind-heat storage system to supply nearby households with heat when needed. Battery and gas storage systems can also absorb surplus electricity or the hydrogen produced from it. As the name “hybrid power plant” suggests, all 1,100 facilities are interconnected via dedicated electricity, gas and hydrogen pipelines. They are digitally monitored and centrally controlled from the control center. The internal power grid alone covers 660 kilometers.
The electrolysis plant, along with the control center, is one of the main attractions of the half-day tour. The route through the area of the decentralized “power plant” is taken by electric car, along narrow country roads between fields of rapeseed and grain, sugar beets and cabbage. Kites and buzzards circle in the sky; sometimes a falcon can be seen hovering over a field. In this idyllic landscape stands an industrial hall housing what Enertrag claims is the world’s first “hydrogen hybrid power plant.” It consists of a combination of three wind turbines, an electrolyzer and a biogas plant with two combined heat and power units that can run on a mixture of biogas and hydrogen. The hybrid power plant, which is part of the overall hybrid power plant system, also includes three large, cigar-shaped H2 tube storage tanks in front of the industrial hall.
Alkaline electrolyzer in operation since 2011 The tour continues inside the building to view the alkaline electrolyzer at its place of origin. The 560-kW unit is the particular pride of Nico Vollack, head of gas and hydrogen – not only because he knows practically every screw of it. “When we commissioned it in 2011, green hydrogen wasn’t even a topic in the public debate,” he reports. “We assembled the electrolyzer ourselves here, so it’s a one-off.” Back then, everything was done by hand, and planning, assembly and commissioning took two and a half years. Vollack points to the hoses filled with potassium hydroxide solution and explains the water-splitting process using a single electrolysis cell, which he holds in his hand for demonstration: a steel frame with a polymer membrane. Seventy such cells are located in the water tank of the electrolyzer, and a voltage of 140 volts DC is applied to them. “So far, we haven’t had to replace any of the membranes,” Vollack explains, sounding almost a little surprised. “But at some point, that will be necessary.”
Electrolysis takes place at a temperature of 70 to 75 degrees Celsius. At full load, the plant produces around 125 m3 of hydrogen per hour. The electricity comes from three nearby 2.3-MW wind turbines, which also went into operation in 2011. They are connected to the rectifier room in the hydrogen plant via underground cables. “If the wind turbines don’t supply electricity, the electrolysis plant also comes to a standstill,” says Vollack.
According to Enertrag, the electrolysis is operated in a grid-supportive manner. If electricity cannot be fed into the grid, it is used for water splitting or directed to a power-to-heat system. However, it is not always possible to prevent wind turbines from being curtailed. Regulatory constraints still stand in the way. Even though the company’s goal is to “not waste a single rotation,” wind turbines still have to be shut down, especially on weekends with low consumption when there is also a lot of wind.
Above the water tank of the electrolyzer are the separators for oxygen and hydrogen. After gas purification and quality control, the hydrogen is fed into a small gasometer and then into compressors for compression. At a pressure of up to 40 bar, it is temporarily stored in the tube storage tanks in front of the hall. Each has a capacity of about 1.2 megawatt hours, totaling approximately one week’s production, Vollack explains.
High demand for hydrogen From the tube storage tanks, the hydrogen can be used for reconversion into electricity in the combined heat and power units of the biogas plant. Alternatively, it is compressed using a high-pressure compressor and filled into trailers or cylinder bundles as needed, then sent off in various directions. “We deliver hydrogen to the Heidekrautbahn every day,” says Vollack. Other customers include six fuel cell buses operated by a regional transport company, operators of fuel cell emergency power systems, a fuel cell-powered ship on the Baltic Sea, and the company’s own hydrogen filling station in nearby Prenzlau.
The hydrogen is also fed into the regional natural gas pipeline and offered to customers on a balance sheet basis as green hydrogen; up to two percent is currently permitted by law. In the future, this pipeline is to be fully converted to the climate-neutral energy carrier as part of Germany’s core hydrogen network. There is no demand for the oxygen produced in the process, so it is released into the atmosphere. “If it weren’t for the biogas plant, we could call ourselves a health resort,” jokes plant manager Vollack. The biogas plant emits a noticeable odor. Enertrag has no complaints about a lack of demand for hydrogen. On the contrary: “Demand has increased so much that we can no longer meet it with this electrolyzer alone,” says Vollack. “That’s why we’re building additional plants.”
For the large-scale production of green hydrogen, the company is planning to establish several electrolysis sites in Mecklenburg-Western Pomerania and Brandenburg with a total capacity of around 185 megawatts. This project, known as the East Germany Electrolysis Corridor, is supported by the federal and state governments as an Important Project of Common European Interest (IPCEI). Each electrolyzer is to supply a hydrogen filling station built nearby and also feed into the future core hydrogen network.
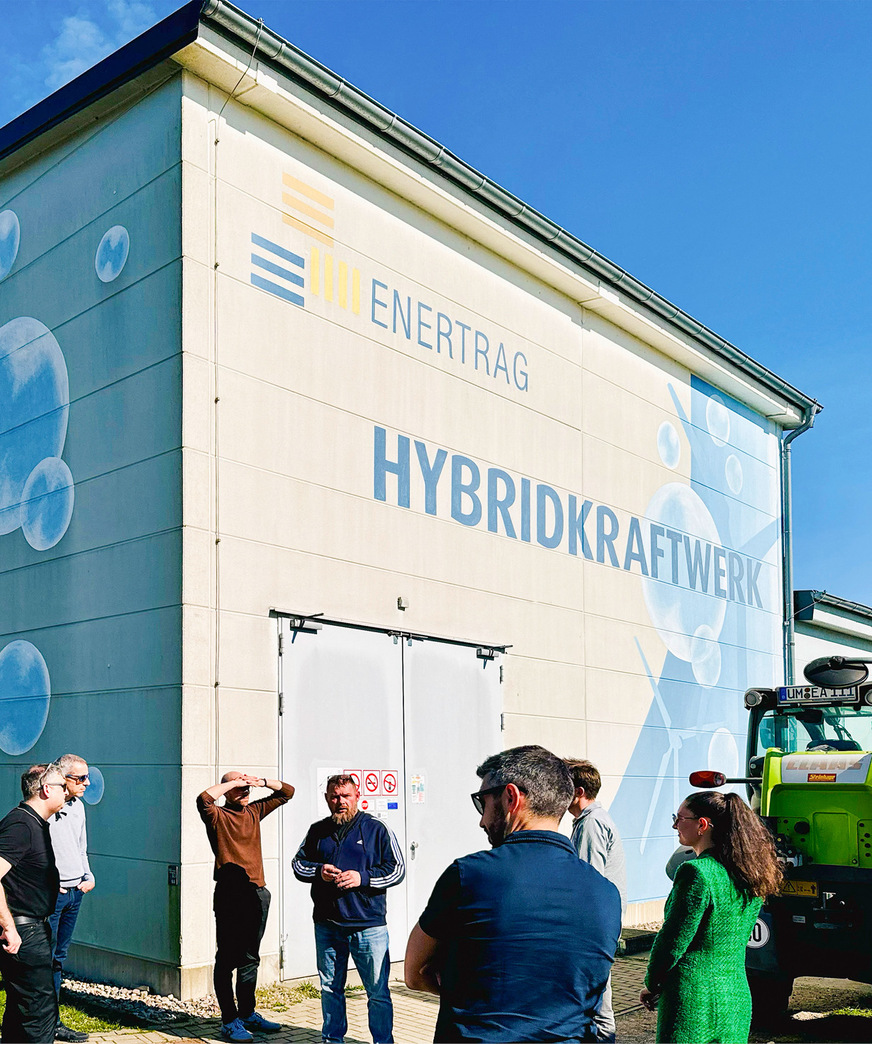
© Monika Rößiger
Dispatchable green electricity on a gigawatt scale The control center in Dauerthal ensures the smooth operation of generation, consumption, storage and transport of all facilities and energy products. It is housed in a circular building with a dark wooden façade that blends into the rural surroundings. “We work here with around 18 people in three shifts, so around the clock,” explains Andreas Grüning, head of remote monitoring. “Data from over a thousand facilities is received here every five to ten minutes and checked in the background by our self-developed power system software.” If anything deviates from the routine, such as underperformance or a signal from a utility company, the remote operators intervene manually. If necessary, they also shut down a wind turbine due to bat activity.
“Through sector coupling – electricity from wind and sun, the production of green hydrogen and heat – we can provide dispatchable capacity on a gigawatt scale,” Grüning continues. “We offer all the key system services of a conventional power plant, from the provision of balancing power to black start capability.” In this way, the hybrid power plant ensures that more renewable energy can be used in the overall system while maintaining grid stability. The wind-heat storage system in Nechlin also absorbs surplus wind power and uses a heating element to heat water. The warm water is stored and supplies 35 households with climate-neutral heat.
The Swiss visitors leave the control center and take a look around Enertrag’s headquarters. The company’s history began in the late 1990s in the historic manor house opposite the control center with the construction of a few wind turbines. The project developer and operator of wind power plants has since become an energy supplier with more than 1,200 employees on four continents. The modern office building next to the manor house is equipped with solar modules, as are the control center and a former farmhouse opposite, which now serves as the company canteen. The group then heads to the final stop on the tour: the Cremzow battery storage facility. “With a capacity of 34.8 MWh, it helps to balance fluctuations in the power grid,” explains Andreas Grüning. “And it is well suited for peak load coverage.” The storage system also provides balancing power and other system services. Thanks to its black start capability, it can restore the grid in the event of a power outage.
Dark doldrums can be mitigated by using the battery storage system and reconversion of green hydrogen. According to Enertrag, the company’s own lines, which collect wind and solar power within the hybrid power plant system, help reduce the future capacity requirements of the public grid. This is because the expansion of collection networks between energy facilities is “up to ten times more cost-effective than redundant expansion of the public grid.”
Bolivia shows interest in the concept The experience Enertrag has gained with its prototype in the Uckermark since 2011 is also benefiting other regions and countries. The “Enertrag hybrid power plant” – a registered trademark – is, according to the company, “globally scalable.” Or at least parts of it, such as the proprietary software, which has been used since spring 2024 in Bolivia for remote monitoring and maintenance of wind turbines. In spring of this year, a delegation from the Bolivian government visited the hybrid power plant and electrolyzer in the Uckermark because they want to implement something similar in their own country. “In theory, such hybrid power plants could be built anywhere the necessary combination of technologies is available,” says Professor Detlef Schulz, specialist in electrical energy systems and spokesperson for the working group Hydrogen for the Northern German Energy System. “In addition, purely balance-sheet-based hybrid power plants can be created with generation facilities and storage systems located further apart, which can contribute to stable grid operation within defined spatial balancing boundaries.” However, this requires extensive practical experience in all sub-areas, especially in the hydrogen sector, which Enertrag has already acquired. For the future, Schulz therefore expects that such hybrid power plants will remain the domain of operators of large-scale facilities, for example at sites for the production of steel, chemicals or cement.
The significant role that green hydrogen now plays in Enertrag’s portfolio is evident in ambitious gigawatt-scale projects such as the Hyphen project in Namibia. There, 1.5 gigawatts of electrolysis capacity are to be installed in each of two phases, along with the necessary solar power plants. The goal is to convert the green hydrogen into ammonia and ship it worldwide. In Uruguay and Germany, the company is planning H2 plants to produce climate-friendly aviation fuels.
Enertrag also sees defossilization of shipping and port logistics as a future business area, which is why the company opened a new office in Hamburg in the fall of last year (see H2international No. 1-2025). Just a stone’s throw from the Chamber of Commerce and the City Hall of the Hanseatic city, Enertrag moved into the top floor of the historic Laeiszhof building, which also houses the H2 Global Foundation and the F. Laeisz Group. Enertrag is already cooperating with Laeisz in the field of climate-neutral methanol and ammonia. In addition, the Port of Hamburg, with its infrastructure, “offers ideal conditions to serve as a hub for the import and export of hydrogen and its derivatives,” said Gunar Hering, CEO of Enertrag, at the office opening.
“The hydrogen ramp-up is in full swing,” summarizes a company spokesperson. “What we need most from policymakers now is reliability. A retreat from expansion targets for renewable energy or hydrogen would jeopardize the entire value chain.” The key now is to remove obstacles – for example in market design. More flexibility in the system would already enable cost-efficient hydrogen production. 
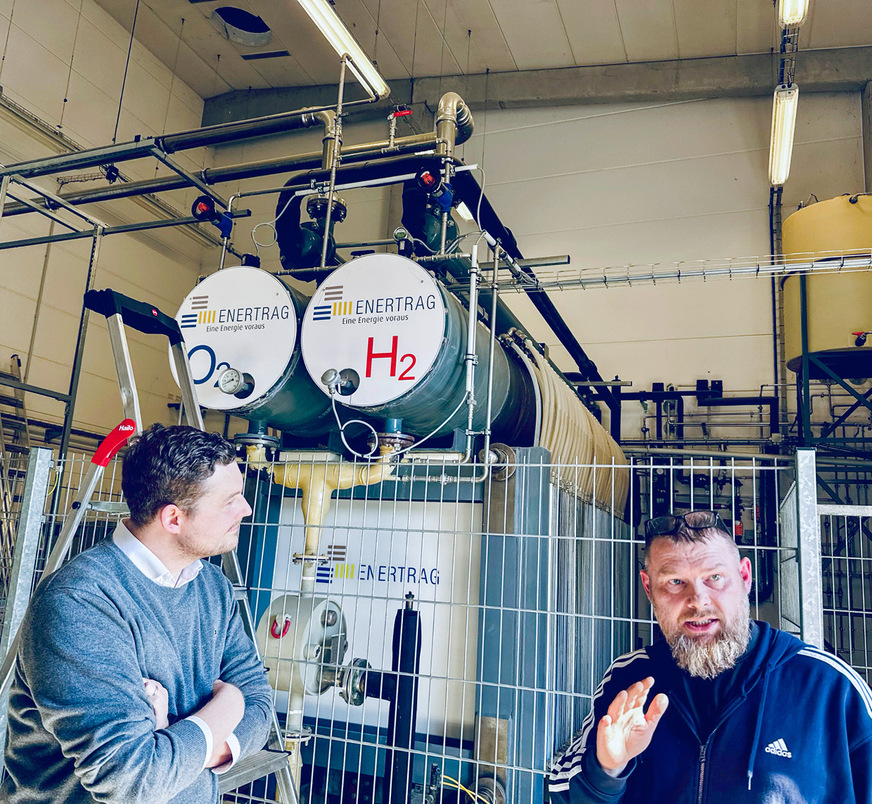
© Monika Rößiger